Why proper curing is essential for high-quality best THCA flower?
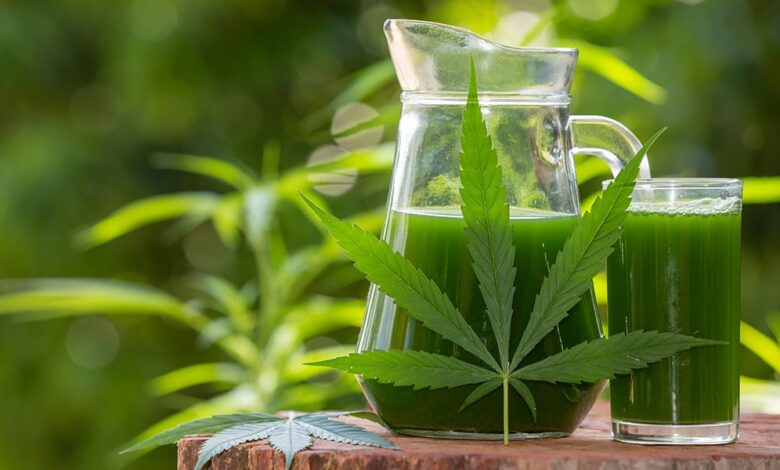
Starting from seed to final product requires precision, timing, and dedication. The curing stage is a fundamental phase that determines the characteristics and excellence of the result. When cultivators start the curing process, they establish specific parameters matching seasonal variations. Setting up dedicated spaces allows strict monitoring of vital measurements throughout each step. Expert growers maintain optimal conditions by adjusting temperature settings between distinct phases.
Traditional and modern techniques
Ancient practices combined with current innovations establish reliable curing standards. Small batches receive individualized attention, where growers check progress daily. Room conditions stay stable using specialized equipment, preventing unwanted moisture buildup or dryness.
Critical timing elements
The initial drying phase lasts 10-14 days under regulated circumstances. Weekly assessments track moisture content reduction. Experienced cultivators recognize subtle changes indicating proper progression.
Essential monitoring points:
- Temperature range maintenance
- Moisture level tracking
- Air circulation patterns
- Container selection criteria
- Duration between rotations
Internal processes
Chemical reactions continue throughout curing, transforming compounds naturally. Sugar molecules break down gradually while chlorophyll diminishes. The best thca flower develops enhanced characteristics when these reactions are correctly completed.
Creating ideal environments
Specialized rooms incorporate precise climate regulation systems. Filtered air maintains cleanliness while preventing contamination risks. Constant circulation ensures even conditioning throughout storage areas.
Documentation practices
Recording detailed measurements helps maintain consistency across batches. Daily logs track environmental readings and any adjustments made. This information guides future improvements and maintains quality standards.
Preservation methods after completion
Once curing finishes, proper storage extends shelf life significantly. Glass containers protect against external factors while maintaining freshness. Regular checks confirm the continued stability of cured products.
Benefits of complete curing
Physical structure improvements develop during proper curing phases. Natural enzymes work continuously, refining internal compositions. Complete curing allows full expression of desired traits.
Quality verification steps:
- Physical appearance assessment
- Moisture content verification
- Structure examination
- Aroma development tracking
- Preservation confirmation
Storage considerations
Dedicated storage areas maintain stable conditions post-curing. Temperature-controlled environments prevent degradation issues. Proper container selection matches specific preservation needs.
Mastering timing elements
Experience guides decisions about curing duration adjustments. Seasonal factors influence specific timing requirements. Regular monitoring determines exact completion points.
Equipment essentials
Professional curing requires reliable measurement tools. Precise gauges track essential environmental factors. Quality equipment ensures accurate readings throughout processes.
Final excellence checks
Multiple testing points confirm proper curing completion. Physical examinations verify desired characteristics development. Documentation reviews ensure all parameters stay within requirements. Purpose-built spaces support proper curing processes. Advanced filtering systems maintain clean environments. Temperature regulation equipment provides consistent conditions.
Continuous improvement
Regular evaluation identifies potential enhancement opportunities. Updated techniques incorporate proven innovations. Staff training ensures consistent implementation of proper procedures. Scheduling accommodates proper curing time requirements. Production planning includes adequate curing capacity. Space allocation matches anticipated volume needs.
Expert knowledge application
Trained staff recognizes crucial transition points. Experience guides timing decisions for each phase. Professional judgment determines necessary adjustments. Quality expectations establish minimum curing requirements. Industry standards guide proper procedure implementation. Regular updates incorporate new proven practices.
Final product excellence depends heavily on proper curing execution. When cultivators follow established procedures precisely, results meet the highest quality standards. This systematic approach ensures reliable outcomes batch after batch.